Top Brands: Sphero - Wonder Workshop - Makeblock - Amazon Kids
BLACK FRIDAY: Amazon Fire Kids Pro 10"
BLACK FRIDAY: Amazon Fire Kids Pro 10"
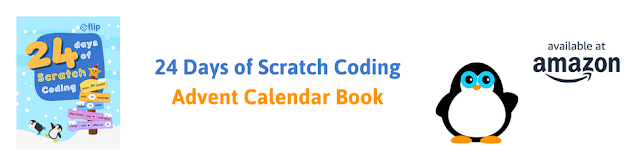
NEWS$show=/search/label/news
Here's where you'll find all the latest news about technology for children. We love to follow cool new inventions on Kickstarter and we hunt out all the latest announcements about tech toys and gadgets for the coming Christmas holidays. You'll also get our take on children's technology stories in the media.
REVIEWS$show=/search/label/review
Our kids technology product reviews are intended to help you work out whether a toy, gadget or kit is a good fit for your child or family.
There's lots of cool stuff available, but is it the right choice for the child or teenager that you are buying for?
We'll help you make the right choices and get the best value for money.
GIFT GUIDES$show=/search/label/gift%20guide
Parents, grandparents, aunts, uncles, and friends assemble. We create gift lists to help you make good choices for kids technology which helps them develop the right skills for the future. We research the best in Coding Toys and Games, Making / Craft Tools and Kits, STEM/STEAM related gifts, Programmable Robots, Electronics Kits and Gadgets for Tech Age Kids and Teens.
PROJECTS$show=/search/label/project
Get crafty with technology. Here we'll post all our ideas and projects using technology to get creative and making with kids. You'll find anything from making a lemon battery to a glow-in-the-dark Minecraft sword. Our projects are tried and tested on our own kids or at events we run, so we are sure you can have a go at home with your kids. Some of our projects use specific tech gadgets which we provide links for you to purchase.
STEM$show=/search/label/stem
STEM stands for Science, Technology, Engineering, and Mathematics. In recent years there is an increased focus in these areas of study. We like to include Art and Design too, so we often talk about STEAM (A stands for Art). At Tech Age Kids we believe Coding is a new literacy and children need to understand how technology works, practice making skills and grow in their curiosity to make a better future for us all.
CODING$show=/search/label/coding
Coding is increasingly being recognised as an important skill for children to learn. Some will learn to code at school or at a coding club, but it's brilliant if they get support at home too.
ELECTRONICS$show=/search/label/electronics
We think it's really important for kids to get hands-on with electronics and learn how to make circuits and write code to control hardware.
Younger kids can start with conductive playdough. For kids who like to combine craft and tech, littleBits are fab. And we love SAM Labs wireless electronics components for making it easy for kids to make Internet of Things inventions.
Lots of electronics kits for kids have support for the Arduino microprocessor environment. The DuinoKit Jr is one of our favourites. Arduino is a fab skill for older kids and teens to develop.
ROBOTICS$show=/search/label/robotics
We love robots at Tech Age Kids, especially programmable ones. We've got lots of them and write reviews and projects that use them.
Our programmable robots for kids buying guide is a good place to start if you're not sure what's available.
Roby the mBot Meccano robot dog is one of our popular projects and has been with us to lots of events. Our Ozobot LEGO trailer is fab for kids who love LEGO and robots.
MAKING AND CRAFT$show=/search/label/making
We're advocates of the creative use of technology, but this needs to be balanced with developing physical skills such as papercraft, woodwork, clay modelling, technical drawing and soldering. If children don't develop these skills as they grow up then physical making projects can become frustrating rather than fun.
The Maker Community uses the term 'making' as a broad term to include all sorts of artisan skills or craft activities. Being able to make things can lead to life-long hobbies or even careers. It's a great feeling to be able to take a project from an idea in your head to a real object that does something.
We're particularly interested to explore products that combine maker skills with tech skills such as electronics but others focus purely on the physical making skills that are still important to modern making.
Arckit is a fab architectural construction kit for older children and adults. It's great for STEAM education and maker families. The Arckit description says "Arckit can work as a stand alone model building system while also becoming a platform to 'Build Off' using your own bespoke 3D printed components or traditional materials." Well that sounds like a challenge!
One of the things my younger son noticed was that you can't put flat floor tiles at the edges of internal floors as the walls get in the way. We thought we'd have a go at 3D printing internal floors so that we could have coloured floors or stick Arckit stickers on top to easily create different flooring effects.
What is Arckit?
Arckit is an architectural construction tool for older children to use as a learning tool and for architects to use as a professional modelling tool. It comes in classic white and clear as well as bright colours.
Arckit is a fantastic base for STEAM projects as you get a professional looking result (yeah cardboard boxes are fun too, but sometimes ...)
Beetle Blocks
I wanted this to be a project that the kids could understand so I decided to try out the Beetle Blocks graphical 3D modelling tool with my 8 year old. Beetle Blocks allows you to model 3D structures using graphical drag and drop commands. It's kid friendly and runs in the browser so you don't have to download anything.Designing the Floors

We drew a quick sketch on the back of an envelope (literally) and my son worked out the dimensions of the 'cuboid' that would act as the floor. Beetle Blocks works in mm. The Arckit walls have a piece at the bottom that comes into the room so you need to allow for this. My son calculated the dimensions of the square we would need for a 2x2 floor.
Each Arckit square measures 25mm (and corresponds to 1.2m in real life) so a 2x2 floor needs a 'carpet' of 25*2 - 10 = 40 mm.<
We made the depth of the floor match the height of the inner tabs on the Arckit walls so we could place furniture against the walls. We could have made it lower but then we wouldn't be able to place furniture flush against the walls.
Coding
It's easy to draw a cuboid with specific dimensions in Beetle Blocks.Then we manually calculated the positions of squares to slot into the squares on the floor of ArcKit. We did this together as it was a little bit tricky, but my son was able to understand it.
We ran the code in Beetle Blocks to see what it would look like and fixed any problems. Initially we didn't realise that the cuboids are centered around the Beetle (current position) and needed to account for that.
Beetle Blocks is so easy to work with as you can see the result immediately and quickly fix any mistakes.
3D Printing and Refining
Once we were happy with the model we exported to STL and 3D printed it. We used yellow as it was already on the printer and is nice and bright so it will show up clearly. Obviously you could use something more subtle like white or clear filament.We tried a test print and found that the floor was slightly too large. We wanted to have enough clearance to make sure that the floor wouldn't push the walls out and put pressure on the connecting pins.
We also found that the print had a few knobbly bits that needed filing off - easy enough to do with PLA plastic.
We adjusted the model to use a slightly smaller cuboid for the outline and reprinted, again filing off any overextruded bits. Success! We had a 2 x 2 floor that could be placed inside a 2 x 2 room with walls and a roof.
Parameterizing the Code
We adapted the code to create a parameterized block which takes the number of x and y grid squares and generates a floor to fit. I had to help my son with this as he hadn't used parameters before but be quickly got the idea. We worked on the maths together.Next we tried a 4 x 4 grid. This was on a printer without a heated print bed and it came out a little bit warped. But this didn't seem to matter too much. Again we needed to file off a few bits that were over-extruded. But then it was possible to push to floor into place and have it stay reasonably flat. If this hadn't worked we would have placed the 3D printed part in warm water to make it pliable and then flattened it. As it was the result was good enough.
We found that one the floors have been pushed into place they stay firm even if you turn the building upside down. The PLA plastic is very soft compared with Arckit pieces.
If you try this project you may need to adapt it to your printer. You'll need your printer to be well calibrated as the tolerance is pretty small on a project like this. Alternatively you can scale the model before printing. We'd recommend starting with a small 2 x 2 floor first and getting that working well.
My son of course loved that he could make a 100 x 100 floor on screen just by changing the parameters. Printing floors is limited by the size of your print bed and how big you can print flat surfaces, though you can always break up a large floor into parts and could write code to help with that.
Arckit also has curved floors and walls and you can create interesting non-rectangular designs. We'll have a look at creating floors for rooms using those in a future project.
Adding Floor Stickers
A 3D printed floor panel acts as a good base for applying Arckit stickers to an internal room. For this purpose you'd want to print using white or clear filament.These floors were created by 3D printing 3x4 bases and then adding Arckit adhesive stickers cut to size.
Verdict
This was a great STEAM project that used lots of skills. My 8 year old got to do some practical maths and learn how to use his coding skills to create models for 3D printing. Creating 3D models programmatically can actually be easier for kids with good maths and spatial awareness than using a visual design tool where you often have to do a lot of precision mouse work to create accurate models and it can be hard to make changes.

/fa-fire/ MONTH TRENDING$type=list
-
At Tech Age Kids we've been testing and writing about kids coding toys for over 10 years. This post is our round up of the current optio...
-
I asked my kids what they wanted to do, other than playing Minecraft, over a long weekend. Not that I didn't want them playing Minecraf...
-
Kiddle, a new search engine for kids has been getting a lot of press attention recently. First came the articles that repeated Kiddle...
/fa-calendar/ RECENT$type=blogging$m=0$cate=0$sn=0$rm=0$c=3$va=0
- 2013
- 2023
- 3d printing
- 3DTin
- accessories
- activities
- adafruit
- advent calendar
- adventure games
- amazon
- amazon fire
- amazon prime
- android
- angry birds
- animation
- anki
- app
- app toy
- app toys
- appcessories
- apple
- apps
- arcbotics
- architecture
- arckit
- arduino
- art
- artificial intelligence
- astronauts
- astronomy
- augmented reality
- automaton
- awards
- battle bots
- battling robots
- bedtime
- big kids
- big tablets
- bigtrak
- bike
- binary
- birthday
- bitsbox
- black friday
- blockly
- blogging
- bloxels
- bluetooth
- board games
- book
- books
- boolean box
- breadboard
- bricks
- brixo
- buying guide
- camera
- cameras
- card game
- careers
- catroid
- celebration
- cellphone
- ces
- chemistry
- chess
- christmas
- circuit cubes
- circuit playground
- circuit scribe
- cleaning
- climbing
- code clubs
- code-a-pillar
- codebug
- coder
- coding
- cognitive learning
- communication
- comparison
- competition/challenges
- computational thinking
- computer
- computer games
- computer science
- computer vision
- computers
- computing
- conductive playdough
- connected toys
- construction
- conversational ai
- cozmo
- craft
- craft cutter
- creative thinking
- creativity
- crochet
- crowdfunding
- css
- cubs
- curiosity
- curious chip
- cyber monday
- dads
- data
- deals
- dens
- design
- design process
- design thinking
- digital parenting
- digital skills
- disability
- disney infinity
- dog tech
- dolls
- drawing
- drones
- duinokit
- earth day
- Easter
- ebooks
- eco
- edblocks
- edison
- edtech
- education
- egypt
- electricity
- electronic pets
- electronic toys
- electronics
- electronics kit
- electronics kits
- electtronics
- elementary
- elenco
- energy
- engineering
- entertainment
- ereader
- ereaders
- esafety
- escape the room
- event
- ewriter
- exercise
- family
- family tech
- fathers day
- Festival of Code
- fiction
- fire
- fitbit
- fitness
- fitness tracker
- flotilla
- flow charts
- flutterbye fairy
- flying
- force awakens
- force friday
- future
- gadgets
- games
- games console
- games consoles
- gaming
- gift guide
- gifts
- girls
- giveaway
- glow in the dark
- grace hopper
- grove
- hackaball
- hacksoton
- halloween
- halloween costumes
- hardware
- headphones
- health
- hexbug
- hexbug aquabots
- hexbug project
- high school
- history
- home
- home education
- homeschool
- hot toys
- hour of code
- html
- humanoid
- ICT
- in app purchasing
- indiegogo
- industry event
- innotab
- innotab 3
- innotab 3s
- internet access
- interviews
- invention
- ios
- IoT
- ipad
- ipad mini
- iphone
- jacquard
- japan
- java
- javascript
- k'nex
- k'nex robotics
- kano
- keyboard
- kickstarter
- kids
- kindle
- kindle fire
- kit
- kits
- kodu
- kubo
- label printer
- languages
- laptop
- laptops
- last minute
- leap motion
- leapfrog
- leappad
- leappad 2
- leappad ultra
- leappad2
- leapreader
- learning
- learning resources
- learning tablet
- learning tablets
- leds
- lego
- lego boost
- lego chain reactions
- lego mindstorms ev3
- lego power functions
- lego technic
- lego wedo
- let's start coding
- lights
- lightseekers
- little kids
- littlebits
- logiblocs
- logic
- logical thinking
- loom
- machines
- magnetic
- make it
- makeblock
- makedo
- maker
- makey makey
- making
- mardles
- mars
- mars rover
- marty
- math
- maths
- mbot
- mbot ranger
- me arm
- meccano
- meccanoid
- meccanoid 2.0
- merge vr
- mews
- michael faraday
- micro:bit
- microbit
- microcontroller
- microscope
- microsoft
- middle school
- miles kelly
- mindstorms
- minecraft
- minecraft mods
- mixed reality
- mobile
- modular electronics
- monsters university
- morse code
- mothers day
- motion capture
- motors
- mover kit
- movie
- movies
- mu
- mu toys
- munzee
- music
- my first robot
- national dog day
- nature
- new
- new year
- news
- news coding
- nikola tesla
- nintendo
- nintendo switch
- ohbot
- ollie
- on the web
- opinion
- origami
- osmo
- outdoors
- ouya
- ozobot
- papercraft
- paperwhite
- parental controls
- parenting
- parrot
- pc
- people
- pet tech
- pets
- phone
- photography
- photon
- physics
- pi day
- picks
- pimoroni
- pinoccio
- pixel kit
- pixelart
- play
- playstation 4
- plezmo
- pocket code
- pocket money
- pokemon
- pokemon go
- poll
- pre order
- pre-teens
- prehistory
- preschoolers
- primary
- printable
- products
- professor einstein
- programming
- project
- projects
- puzzles
- python
- racing
- raspberry pi
- reading
- reivew
- remote control
- research
- resource
- resources
- retro
- review
- rights
- robot
- robot dog
- robot fish
- robot wars
- ROBOTERRA
- roboticals
- robotics
- robots
- role models
- role play
- romo
- romotive
- root
- rover
- safety
- sam labs
- samuel morse
- sandbox
- schools
- science
- scratch
- scratchjr
- screen time
- screenless
- screens
- sensors
- servos
- simbrix
- skills
- skylanders
- skylanders superchargers
- skylanders swap force
- smart pens
- smartphone
- smartwatch
- snap circuits
- social media
- solar power
- soldering
- sonic pi
- sony koov
- sound
- space
- sparki
- speaker
- speech sythesis
- sphero
- sphero mini
- spider
- star wars
- stars
- STEAM
- stem
- stikbot
- stop motion
- stop motion studio
- storage
- story
- strawbees
- students
- subscription
- subscriptions
- sugru
- summer
- swift
- tablet
- tablets
- tangible coding
- tech
- tech age
- tech craft
- tech is bad
- tech is good
- tech toys
- tech will save us
- technology
- technology will save us
- teens
- teknikio
- tekno
- teksta
- tenka labs
- tesla
- textiles
- thames & kosmos
- the extraordinaires
- tim berners lee
- tinkercad
- tinybop
- toddlers
- toot-toot
- top pick
- touch
- toy
- toys
- travelling
- TTS
- TV
- tween
- tweens
- tynker
- typing
- ux
- vehicles
- videos
- view-master
- views
- virtual reality
- voice assistants
- voice recognition
- vr
- vtech
- web
- websites
- wifi
- wii
- wii u
- windows 8
- wonder workshop
- wowwee
- writing
- writing. education
- xbox one
- xyzprinting
/fa-dice/ RANDOM$type=blogging$m=0$cate=0$sn=0$rm=0$c=3$va=0$src=random-posts
- 2013
- 2023
- 3d printing
- 3DTin
- accessories
- activities
- adafruit
- advent calendar
- adventure games
- amazon
- amazon fire
- amazon prime
- android
- angry birds
- animation
- anki
- app
- app toy
- app toys
- appcessories
- apple
- apps
- arcbotics
- architecture
- arckit
- arduino
- art
- artificial intelligence
- astronauts
- astronomy
- augmented reality
- automaton
- awards
- battle bots
- battling robots
- bedtime
- big kids
- big tablets
- bigtrak
- bike
- binary
- birthday
- bitsbox
- black friday
- blockly
- blogging
- bloxels
- bluetooth
- board games
- book
- books
- boolean box
- breadboard
- bricks
- brixo
- buying guide
- camera
- cameras
- card game
- careers
- catroid
- celebration
- cellphone
- ces
- chemistry
- chess
- christmas
- circuit cubes
- circuit playground
- circuit scribe
- cleaning
- climbing
- code clubs
- code-a-pillar
- codebug
- coder
- coding
- cognitive learning
- communication
- comparison
- competition/challenges
- computational thinking
- computer
- computer games
- computer science
- computer vision
- computers
- computing
- conductive playdough
- connected toys
- construction
- conversational ai
- cozmo
- craft
- craft cutter
- creative thinking
- creativity
- crochet
- crowdfunding
- css
- cubs
- curiosity
- curious chip
- cyber monday
- dads
- data
- deals
- dens
- design
- design process
- design thinking
- digital parenting
- digital skills
- disability
- disney infinity
- dog tech
- dolls
- drawing
- drones
- duinokit
- earth day
- Easter
- ebooks
- eco
- edblocks
- edison
- edtech
- education
- egypt
- electricity
- electronic pets
- electronic toys
- electronics
- electronics kit
- electronics kits
- electtronics
- elementary
- elenco
- energy
- engineering
- entertainment
- ereader
- ereaders
- esafety
- escape the room
- event
- ewriter
- exercise
- family
- family tech
- fathers day
- Festival of Code
- fiction
- fire
- fitbit
- fitness
- fitness tracker
- flotilla
- flow charts
- flutterbye fairy
- flying
- force awakens
- force friday
- future
- gadgets
- games
- games console
- games consoles
- gaming
- gift guide
- gifts
- girls
- giveaway
- glow in the dark
- grace hopper
- grove
- hackaball
- hacksoton
- halloween
- halloween costumes
- hardware
- headphones
- health
- hexbug
- hexbug aquabots
- hexbug project
- high school
- history
- home
- home education
- homeschool
- hot toys
- hour of code
- html
- humanoid
- ICT
- in app purchasing
- indiegogo
- industry event
- innotab
- innotab 3
- innotab 3s
- internet access
- interviews
- invention
- ios
- IoT
- ipad
- ipad mini
- iphone
- jacquard
- japan
- java
- javascript
- k'nex
- k'nex robotics
- kano
- keyboard
- kickstarter
- kids
- kindle
- kindle fire
- kit
- kits
- kodu
- kubo
- label printer
- languages
- laptop
- laptops
- last minute
- leap motion
- leapfrog
- leappad
- leappad 2
- leappad ultra
- leappad2
- leapreader
- learning
- learning resources
- learning tablet
- learning tablets
- leds
- lego
- lego boost
- lego chain reactions
- lego mindstorms ev3
- lego power functions
- lego technic
- lego wedo
- let's start coding
- lights
- lightseekers
- little kids
- littlebits
- logiblocs
- logic
- logical thinking
- loom
- machines
- magnetic
- make it
- makeblock
- makedo
- maker
- makey makey
- making
- mardles
- mars
- mars rover
- marty
- math
- maths
- mbot
- mbot ranger
- me arm
- meccano
- meccanoid
- meccanoid 2.0
- merge vr
- mews
- michael faraday
- micro:bit
- microbit
- microcontroller
- microscope
- microsoft
- middle school
- miles kelly
- mindstorms
- minecraft
- minecraft mods
- mixed reality
- mobile
- modular electronics
- monsters university
- morse code
- mothers day
- motion capture
- motors
- mover kit
- movie
- movies
- mu
- mu toys
- munzee
- music
- my first robot
- national dog day
- nature
- new
- new year
- news
- news coding
- nikola tesla
- nintendo
- nintendo switch
- ohbot
- ollie
- on the web
- opinion
- origami
- osmo
- outdoors
- ouya
- ozobot
- papercraft
- paperwhite
- parental controls
- parenting
- parrot
- pc
- people
- pet tech
- pets
- phone
- photography
- photon
- physics
- pi day
- picks
- pimoroni
- pinoccio
- pixel kit
- pixelart
- play
- playstation 4
- plezmo
- pocket code
- pocket money
- pokemon
- pokemon go
- poll
- pre order
- pre-teens
- prehistory
- preschoolers
- primary
- printable
- products
- professor einstein
- programming
- project
- projects
- puzzles
- python
- racing
- raspberry pi
- reading
- reivew
- remote control
- research
- resource
- resources
- retro
- review
- rights
- robot
- robot dog
- robot fish
- robot wars
- ROBOTERRA
- roboticals
- robotics
- robots
- role models
- role play
- romo
- romotive
- root
- rover
- safety
- sam labs
- samuel morse
- sandbox
- schools
- science
- scratch
- scratchjr
- screen time
- screenless
- screens
- sensors
- servos
- simbrix
- skills
- skylanders
- skylanders superchargers
- skylanders swap force
- smart pens
- smartphone
- smartwatch
- snap circuits
- social media
- solar power
- soldering
- sonic pi
- sony koov
- sound
- space
- sparki
- speaker
- speech sythesis
- sphero
- sphero mini
- spider
- star wars
- stars
- STEAM
- stem
- stikbot
- stop motion
- stop motion studio
- storage
- story
- strawbees
- students
- subscription
- subscriptions
- sugru
- summer
- swift
- tablet
- tablets
- tangible coding
- tech
- tech age
- tech craft
- tech is bad
- tech is good
- tech toys
- tech will save us
- technology
- technology will save us
- teens
- teknikio
- tekno
- teksta
- tenka labs
- tesla
- textiles
- thames & kosmos
- the extraordinaires
- tim berners lee
- tinkercad
- tinybop
- toddlers
- toot-toot
- top pick
- touch
- toy
- toys
- travelling
- TTS
- TV
- tween
- tweens
- tynker
- typing
- ux
- vehicles
- videos
- view-master
- views
- virtual reality
- voice assistants
- voice recognition
- vr
- vtech
- web
- websites
- wifi
- wii
- wii u
- windows 8
- wonder workshop
- wowwee
- writing
- writing. education
- xbox one
- xyzprinting